Supply Chain Disruption: A Survival Guide
With everything from trade disputes to climate change ready to disrupt the flow of goods, companies need risk mitigation plans to cover a broad range of scenarios.
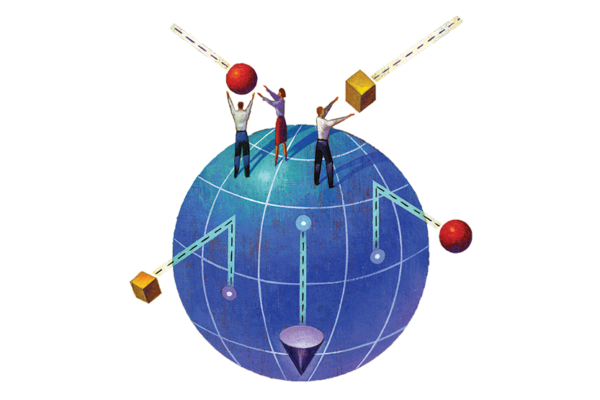
In 2011, when an earthquake and tsunami shuttered factories in northern Japan, companies around the world scrambled to find new sources for auto parts, computer chips, and other crucial components.
In 2018, as the United States and China rolled toward a trade war, some U.S. firms made plans to move production from China to Vietnam, Malaysia, or elsewhere.
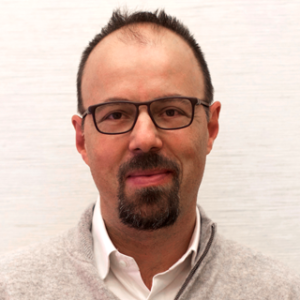
Throw in hurricanes, blizzards, factory fires, strikes and political upheaval — all those disturbances that hit with alarming frequency these days — and one thing is clear: The global economy sails on choppy seas. The next wave of supply chain disruption is always about to crash down, and companies need to plan carefully to deal with a wide variety of risks.
“There is no end to disruption,” says Christian Callieri, MBA ’01, chief supply chain officer at the New York-based fashion company Tory Burch.
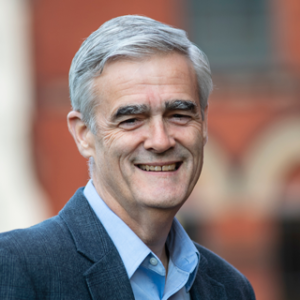
“It’s something we prepare for and build flexibility into our system for,” says Mike Train, MBA ’91, president of Emerson, a global manufacturer based in St. Louis.
Types of Disruption
Executives understand they need to prepare for events that might shut down their own factories or halt the inflow of essential products. But the unpredictable nature of many disruptions makes it hard to tell which Plan B a company may have to roll out next. That’s especially true of natural and man-made disasters. One never knows if the next big shock will stem from wildfires in California, flooding in Thailand, or an explosion at a chemical plant in Texas.

Not only can disaster strike anywhere, at any time, but it’s sometimes hard to tell if one’s own supply chain sits in the path of an oncoming hurricane or on an earthquake fault line. That’s because a supply chain often comprises multiple tiers of trading partners.
“You’re buying parts from a company, and that company is buying parts from yet another company,” says William Schmidt, assistant professor of operations, technology and information management at Johnson. “Some companies’ supply chains go eight, nine, ten levels deep before they get to raw materials.”
Following the Tohoku earthquake and tsunami in 2011, “many companies did not even know they had a second- or third-tier supplier located in that region of Japan.” — Professor Vishal Gaur
Firms that lack information about upstream suppliers can be caught off guard, says Vishal Gaur, associate dean for MBA programs, Emerson Professor of Manufacturing Management, and professor of operations, technology and information management at Johnson. That’s what happened after the Tohoku earthquake and tsunami in 2011. “Many companies did not even know they had a second- or third-tier supplier located in that region of Japan,” he says.
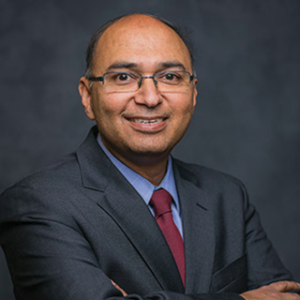
A second kind of supply chain disruption arises from trade disputes. When international agreements break down, as when the United States threatened to toss out the North American Free Trade Agreement (NAFTA), or when countries impose tariffs, that doesn’t literally shut off supplies. But trade disputes do raise prices, changing the calculation about where to source goods.
Tory Burch — which makes its products in Europe, Asia, and the Americas, and sells around the world — was one of many companies that felt the shock when the U.S. hit China with a 10 percent tariff in the summer of 2018. The business had little time to adjust to a sudden jump in the cost of imported small leather goods from China.
“We were surprised by how quickly after the review and comments period the tariffs went up,” says Callieri. “We expected at least another couple of weeks.” Then came another announcement: that those tariffs would rise to 25 percent in January 2019. “That was aligned with our worst-case scenario,” he says.
Tariffs can also change the cost equation for companies that source close to home. For example, as recent U.S. tariffs increased the price of imported aluminum, that allowed smelters in the United States to raise their prices as well, Schmidt says.
Retaliatory tariffs can take their toll as well. “Many U.S. suppliers sell into China, for example,” says Gaur. “When China imposes tariffs, those suppliers may go out of business.” That could leave U.S. buyers with fewer domestic sources.
A third kind of trade disruption stems from port congestion, labor disputes, road blockages, and other events that impede transportation. In recent years, for instance, slowdowns and strikes by longshoremen have delayed the movement of cargo through ports on the U.S. West Coast — ports crucial to global trade. In 2015, labor actions at 29 U.S. ports cost the economy $2 billion per day, according to The Atlantic.
“The port mandated that produce and other products with an expiration date would take precedence. So our goods were stuck.” — Christian Callieri, MBA ’01, chief supply chain officer at Tory Burch
Congestion at a port in northern Brazil once left Tory Burch unable to get product out of that country for three or four weeks, says Callieri. There simply weren’t enough shipping containers to accommodate all the outbound cargo. “The port mandated that produce and other products with an expiration date would take precedence. So our goods were stuck.” Three or four weeks can make the difference between selling a product at full price or having to take end-of-season markdowns, he says.
A fourth source of supply chain disruption derives from questions of social responsibility.
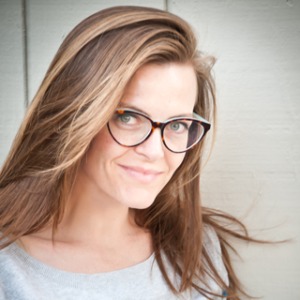
Many industrialized countries have laws prohibiting the import of goods made with child labor, forced labor, or other unethical practices, says Carrie George, MPA ’06, vice president of sustainability solutions at Everledger. A technology startup, Everledger enables companies to use blockchain technology to record details of every transaction in the manufacture and sale of products such as gemstones, minerals, electronics, and art.
Even when a country does not actually punish the import of a product that has a questionable pedigree, if word gets out about such a problem, it could spark a public relations disaster.
Companies concerned about slavery, child labor, corruption, or other moral hazards face the same challenge as companies worried about earthquakes and hurricanes: They don’t always know the suppliers that are upstream in their supply chains. That means they also don’t know the work conditions that go into their products upstream, so they don’t know where their vulnerabilities lie.
Take the example of a chocolate maker that lacks a clear view of its supply chain all the way back to the farmers that grow the cocoa beans, George says. “Let’s say news media or a labor advocacy group reports a case of child labor in Ivory Coast. A company would want to take very quick action to confirm that the case related to their supply chain and then quickly act to ensure remediation.” If the company found instead that the case did not relate to its supply chain, it would want to publicize that fact, and it might still support remediation in the region, to ensure improvements in the industry overall, she says.
To get the facts, a responsible sourcing officer at the candy firm would start talking to the tier 1 and tier 2 suppliers, and then work up through several other tiers, where the company had no direct connections, to learn if child labor played a role in any of its products. If the officer found a problem, rather than drop the supplier outright (leaving it to continue employing children), the candy company typically would try to get the supplier to change its ways, George says.
“This investigation and subsequent remediation take time, cooperation, and tolerance to work through the problems and withstand PR pressure,” George says. The company would also need to spend money to make the necessary improvements.
Before joining Everledger in 2018, George held social responsibility positions at Brilliant Earth, Apple, and J. Crew, where her jobs involved “mapping” supply chains through multiple tiers in search of potential risks and designing programs to address the risks identified.
Product recalls, business failures among suppliers, and many other hazards may also interrupt the flow of products that a company needs.
Strategies for Building Resilience
Whatever spurs a disruption, operations will return to normal faster if a company already has plans in place to mitigate the problem. “You can never prevent the next natural disaster from happening,” says Li Chen, associate professor of operations, technology and information management at Johnson. “But you can make your supply chain more robust, more resilient, so you can recover sooner.”
“You can never prevent the next natural disaster from happening. But you can make your supply chain more robust, more resilient, so you can recover sooner.” — Professor Li Chen
At Emerson, when catastrophic flooding in Thailand severed links in the supply chain, the need for strong mitigation strategies became abundantly clear, Train says. “We want to be able to build the same product line in at least two places in the world, so we get some of that natural backup capability, to be able to shift manufacturing depending on events.”
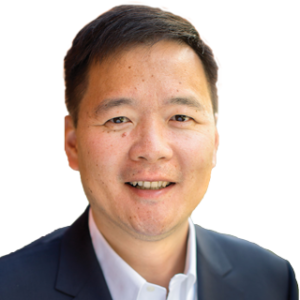
Manufacturing in multiple locations is just one of many practices companies use to insure themselves against future disruptions. Another is sourcing the same components or materials from two or more suppliers. “Hopefully, those suppliers are located in different regions, so you can avoid the potential risk of natural disasters or tariffs,” Chen says. If one supplier suddenly drops out of the picture, a company can simply order more product from the second.
But dual sourcing poses challenges of its own. For one thing, when you buy 50,000 units of a product from each of two suppliers, you won’t get the same volume discount as when you buy 100,000 from one source, says Schmidt. “And then you have to manage those supplier relationships and work out the logistics associated with two different suppliers.” All that adds overhead costs, he says.
Even when a company buys the same component from two suppliers, it still might face a single-sourcing risk. What if those suppliers buy an important subcomponent from a mutual second-tier source? Schmidt says he has seen that dynamic in action. “When the second tier went down, both of the suppliers called in rapid succession, saying, ‘We’ve got a disruption.’”
To avoid such painful surprises, supply chain professionals try to gain a better view of the companies that sit upstream in their supply chains. That was the case with Nkechi Ejimadu, MBA ’15, manager consultant of supply chain strategy at Deloitte’s federal government practice.
“We would ask, ‘Are your second-tier manufacturers getting materials from reliable sources?’” — Nkechi Ejimadu, MBA ’15, manager consultant of supply chain strategy at Deloitte
Before Deloitte, Ejimadu worked in the procurement leadership program at Johnson & Johnson as a strategic sourcing manager for the endosurgery division. As part of her role, she worked with J&J’s Center of Excellence to investigate risk associated with suppliers’ raw material sources. “We would ask, ‘Are your second-tier manufacturers getting materials from reliable sources? Are there any risks that we need to mitigate involving logistics, quality, or cost?’” she says. “‘What is the purity and quality? What is your plan in case of a natural disaster, or a government situation or instability?’” To help mitigate certain risks and prevent business continuity problems, J&J requires suppliers to keep a specific quantity of material on hand, she says.
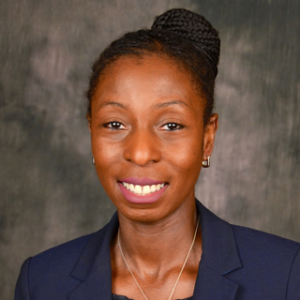
Some suppliers are reluctant to keep material onsite, due to the holding costs and inventory management concerns. But for material that requires a long lead time on orders, for expensive product lines, and for high-risk materials, J&J stands firm on its mitigation requests, Ejimadu says.
Some companies manage risk by making products close to where they sell them, rather than halfway around the world. For instance, Emerson builds product in the Americas for the Americas and in Asia for Asia. While there are many reasons to adopt this strategy, one benefit is that it keeps Emerson from relying too heavily on a small pool of suppliers. “It gives us exposure to suppliers in different parts of the world, so we can nurture those relationships,” Train says.
“A lot of the work we do is about having regional responsiveness and flexibility.” — Mike Train, MBA ’91, president of Emerson
Emerson does use some suppliers on a global basis. “But a lot of the work we do is about having regional responsiveness and flexibility,” Train says. For instance, if a supplier in one part of the world suddenly can’t provide a component, Emerson can ask suppliers in other regions to fill the gap.
If a business can bear the carrying costs, it might stock extra inventory as a hedge against future shortages, Schmidt says. Or if it uses the same component in two products, it might decide that in case of a shortage, it will focus on making the product that sells at a higher margin until new supplies come in.
A company might also do some redesigning, perhaps arranging to use the same materials in multiple products. The company can then stage those materials near factories in several locations, says Callieri. If one plant has to stop operating, the company might compensate by ramping up production elsewhere. “If you haven’t reduced the complexity of your materials, it becomes very difficult to react if something unexpected happens in one location,” he says.
Technology Solutions
Big data and advanced analytics might help a company predict disruptions before they occur and then take preventive action. For instance, an analytic system might detect that one supplier often fills orders slightly late, says Schmidt. “If you can figure that out before your competitors, you may be able to unearth an underlying problem with that supplier before your competitors do and then try to lock up alternative sources of supply before there’s a rush on those other sources.”
Other technology can help as well. Everledger’s service, for example, is designed to provide the kind of detail companies need to monitor their upstream supply chains and address potential moral hazards. “If we can automate that and make it simple, we’ll be able to manage these types of risk and also have improved supply chains,” George says. For instance, a blockchain record would have made it much easier to trace the source of E. coli contamination that shut down sales of romaine lettuce in the fall of 2018, she says.
For certain components — especially parts made of metal or plastic — 3D printing could offer a backup source in case of a supply disruption. While 3D printing is currently too expensive to use in mass production, and mass-printed parts might not meet quality standards, Chen says: “Over the next few years, as the technology matures and the cost goes down, I think we’ll see a mass adoption of the technology.”
Even with a strong view of the upstream supply chain and a solid portfolio of backup plans, a company trying to fortify its supply chain against disruption faces a complex assortment of uncertainties. For example, how long before the strike ends, the flood waters recede, or the damaged plant gets back into business?
“One-week disruptions happen all the time,” says Schmidt. “The trick is, you don’t know if any one disruption is really going to be one week, or if it will wind up being three, four weeks or more.”
3 Comments
Faiza
Very interesting read. Thank you
Sabir Hussain
Very latest and relevance to the current scenario, sourcing officer must focus on this aspect in normal circumstances and plan prototype how to deal in actual happening
Butter john
Thomas Friedman announced that “the world is flat” 15 years ago, considering the many ways in which technology and lower barriers to trade have collapsed national borders and fostered a new era of globalization in which everyone is doing business with everyone else.
But what happens when the president of the United States, the world’s largest economy, imposes steep new tariffs on everything from Chinese steel to French wines on those well-oiled global supply chains? Or when business in China is paralyzed by a fast-spreading virus, with ripple effects on businesses worldwide?
Hau Lee, a professor of operations, information, and technology at Stanford Graduate School of Business, says these natural and manmade disturbances are the chaotic new realities of global supply chains. Globalized procurement is here to stay for most major American producers, as they continue to take advantage of low-cost labor overseas.
That’s a supply chain often why comprises multiple tiers of trading partners?
Comments are closed.